What solutions does Fused Deposition Modeling (FDM) have for manufacturing complex structures?
Release Time : 2024-10-15
Fused Deposition Modeling (FDM) is a common 3D printing technology suitable for manufacturing complex structures.
Support structure design:
Self-supporting design: By optimizing the model design to make it self-supporting, the need for additional support structures is reduced. For example, when using a cantilever structure, it can be designed to be trapezoidal or stepped to reduce stress concentration.
Water-soluble support material: Using water-soluble materials as support structures, it can be removed by water dissolution after printing, which is suitable for complex geometries and fine details.
Multi-material printing:
Functional gradient materials: Use multiple materials in the same printing process to create functional gradient structures. For example, high-strength materials can be used in areas where high strength is required, and elastic materials can be used in areas where flexibility is required.
Color and property switching: By switching materials during the printing process, different colors or physical properties can be created on the same part, which is suitable for applications that require complex markings or functional zoning.
Embedded functional integration:
Embedded electronic components: Embed electronic components such as sensors, wires, etc. during the printing process to create products with integrated electronic functions.
Embedded fluid channels: Through multi-layer printing technology, embedded fluid channels are designed to manufacture complex structures with fluid transmission functions.
Topology optimization:
Bionic design: Using the principles of bionics, find structural inspiration from nature to design complex structures that are both lightweight and high-strength.
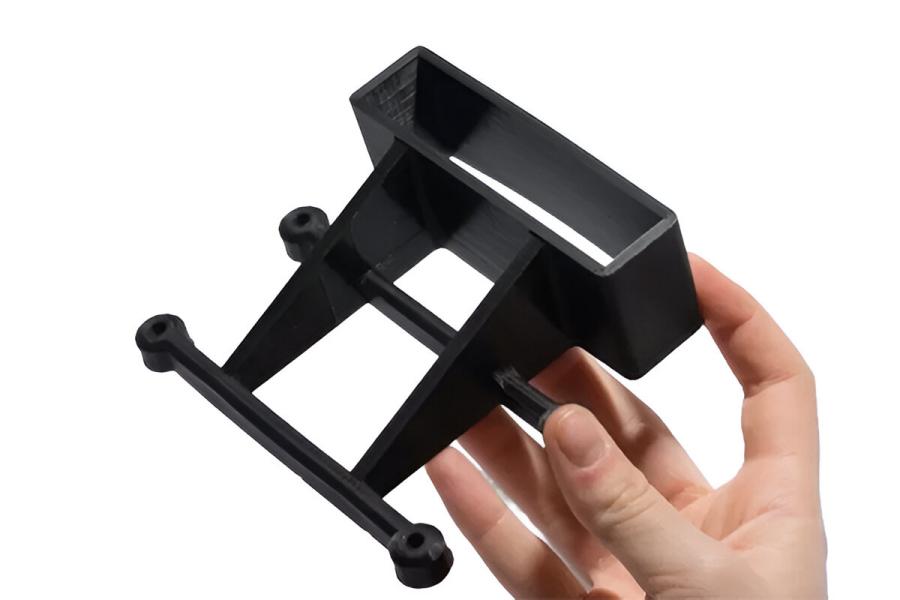
Topology optimization algorithm: Using the topology optimization algorithm in computer-aided design (CAD) software, the optimized structural form is automatically generated to reduce material usage and improve performance.
Multi-axis printing technology:
Tilt printing: By tilting the printing platform or print head, the printing path is optimized, the hanging part is reduced, and the printing effect is improved.
Rotary printing: Using a rotating platform, print parts with complex curved surfaces or annular structures to improve printing accuracy.
Post-processing technology:
Heat treatment: Through heat treatment technology, the mechanical properties and stability of the material are improved, which is particularly suitable for complex structures that require high precision and high strength.
Surface treatment: Use chemical treatment, grinding, spraying and other technologies to improve the surface quality and functionality of printed parts.
Through the above solutions, Fused Deposition Modeling (FDM) technology can provide flexible and diverse options in complex structure manufacturing to meet the needs of different applications.
Support structure design:
Self-supporting design: By optimizing the model design to make it self-supporting, the need for additional support structures is reduced. For example, when using a cantilever structure, it can be designed to be trapezoidal or stepped to reduce stress concentration.
Water-soluble support material: Using water-soluble materials as support structures, it can be removed by water dissolution after printing, which is suitable for complex geometries and fine details.
Multi-material printing:
Functional gradient materials: Use multiple materials in the same printing process to create functional gradient structures. For example, high-strength materials can be used in areas where high strength is required, and elastic materials can be used in areas where flexibility is required.
Color and property switching: By switching materials during the printing process, different colors or physical properties can be created on the same part, which is suitable for applications that require complex markings or functional zoning.
Embedded functional integration:
Embedded electronic components: Embed electronic components such as sensors, wires, etc. during the printing process to create products with integrated electronic functions.
Embedded fluid channels: Through multi-layer printing technology, embedded fluid channels are designed to manufacture complex structures with fluid transmission functions.
Topology optimization:
Bionic design: Using the principles of bionics, find structural inspiration from nature to design complex structures that are both lightweight and high-strength.
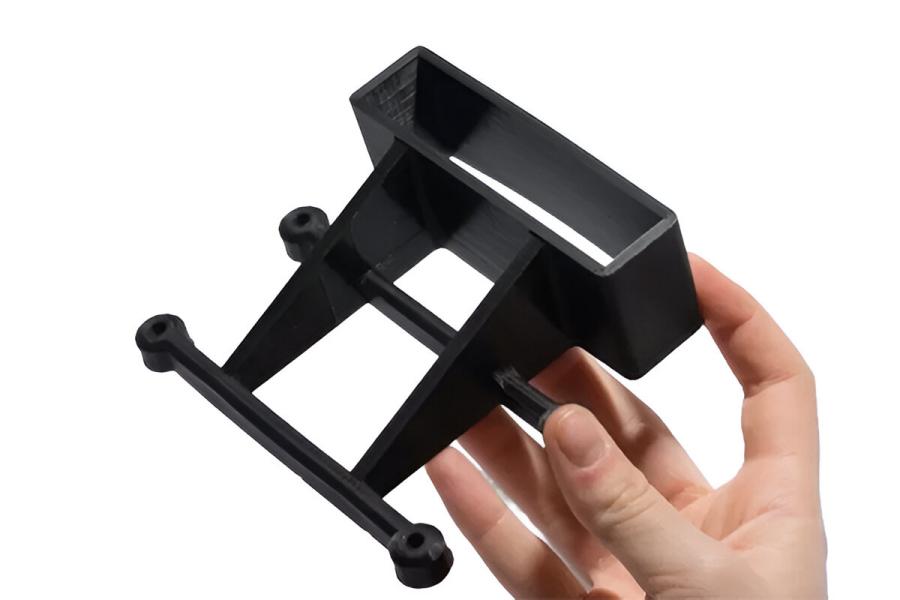
Topology optimization algorithm: Using the topology optimization algorithm in computer-aided design (CAD) software, the optimized structural form is automatically generated to reduce material usage and improve performance.
Multi-axis printing technology:
Tilt printing: By tilting the printing platform or print head, the printing path is optimized, the hanging part is reduced, and the printing effect is improved.
Rotary printing: Using a rotating platform, print parts with complex curved surfaces or annular structures to improve printing accuracy.
Post-processing technology:
Heat treatment: Through heat treatment technology, the mechanical properties and stability of the material are improved, which is particularly suitable for complex structures that require high precision and high strength.
Surface treatment: Use chemical treatment, grinding, spraying and other technologies to improve the surface quality and functionality of printed parts.
Through the above solutions, Fused Deposition Modeling (FDM) technology can provide flexible and diverse options in complex structure manufacturing to meet the needs of different applications.